Damien LHÔTE, Maitre d’œuvre des équipes de Réparations des Ponts Métalliques (R.P.M) de la SNCF, a supervisé la restauration de plusieurs ouvrages d’Eiffel, comme les viaducs de Garabit et de Rouzat. Ses équipes, hautement spécialisées, ont la charge de restaurer les anciens ponts métalliques du réseau ferré, et effectuent ce travail avec passion, dans le strict respect des méthodes de construction d’origine.
Il nous présente dans cet article la technique du rivetage, élément central souvent méconnu des constructions métalliques du XIXéme siècle – la Tour d’Eiffel comptant à elle seule plus de 2.500.000 rivets ! – et nous introduit au travail de ses équipes :
Dans la seconde moitié du XIXe siècle, Gustave Eiffel popularise un nouveau type d’assemblage entre plusieurs pièces métalliques : le rivetage à chaud. Technique présente depuis le début du XIXéme siècle pour la fabrication des machines à vapeur, des chemins de fers, des constructions navales, halles, gares, écluses, monuments, ouvrages d’arts, il va la reprendre à son compte et la pousser plus loin qu’aucun autre: la fameuse Tour Eiffel se compose de 18038 pièces métalliques (cornières, plats métalliques…) mais surtout de 2 500 000 rivets dont les 2/3 ont été assemblés sur site.
Mais savez-vous ce qu’est un rivet et le rivetage?
Un rivet est un élément d’assemblage métallique qui se présente sous la forme d’une tige cylindrique munie d’une tête dite « première » forgée en atelier. La longueur des rivets varie en fonction du nombre et de l’épaisseur des pièces à assembler. La tête seconde ou rivure est forgée sur chantier avec un marteau à main (masse) ou un marteau pneumatique.

Le rivet provient de barres métalliques étirées puis coupées selon la longueur du rivet souhaité. Au début du XIXe siècle, les rivets étaient forgés uniquement à la masse. Le métal destiné à former la tête du rivet (ou tête première), était refoulé sur lui-même par les chocs successifs du marteau. Le forgeron frappait rapidement sur la tête du fer chaud, qui émergeait de la bombarde, refoulant ainsi le métal et achevait la forme de la tête avec la bouterolle, le moule de la tête seconde. Un ouvrier expérimenté pouvait forger, chaque jour, une centaine de kilogrammes de rivets, en atelier.
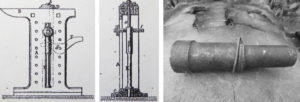
C’est en 1836 qu’Antoine Durenne, chaudronnier, inventa la première machine capable de fabriquer mécaniquement les rivets. Le procédé consiste à refouler le métal sur lui-même, mais cette fois-ci sans choc et par une pression continue à l’aide d’une bouterolle, ce qui permet d’augmenter grandement le rendement de la fabrication de rivets.
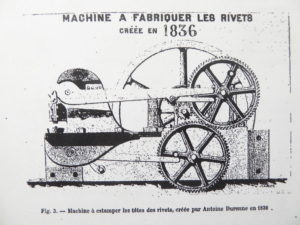
Avant de réaliser le rivetage d’un assemblage, il faut au préalable percer des trous à travers les pièces à assembler de manière à avoir un trou parfaitement aligné. Une fois cette opération réalisée, la forge au charbon ou au fioul peut être mise en route. Les rivets y sont ensuite chauffés à une température supérieure à 1100°C afin d’être posés à une température comprise entre 900 et 950°C. L’opération de rivetage consiste à insérer le rivet dans le trou et de former la tête seconde ou rivure par refoulement de l’acier du rivet, ce qui va ainsi remplir complètement le trou de l’assemblage.
La rivure ou tête seconde se fait au marteau à main ou masse (méthode la plus ancienne) ou au marteau pneumatique appelé « le pétard » (marteau à percussions frappant les rivets à une force de frappe linéaire) équipé d’une bouterolle d’une part et d’une contre-bouterolle ou tas de l’autre côté de l’assemblage.
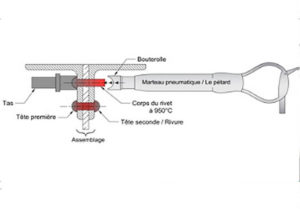
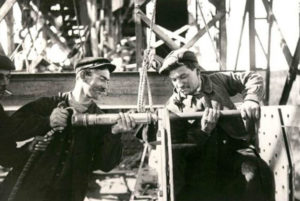
Le rivetage est généralement exécuté par une équipe de 4 ouvriers. Un riveur, un chauffeur de rivets, un teneur de tas et un teneur de bouterolle composent cette équipe.
Les rivets sont chauffés dans une forge à plus de 1100°C jusqu’à l’obtention d’une couleur rouge « cerise ». Dès lors, le chauffeur sort le rivet de la forge à l’aide d’une pince, le frappe au sol afin d’enlever la calamine (croute d’oxydes de fer lors de la chauffe) puis le jette au teneur de bouterolle. Celui-ci prend le rivet et l’introduit dans le trou à remplir et saisit avec une pince le bout du rivet dès que son extrémité sort de l’assemblage pour le maintenir en place. Pendant qu’il installe son tas arc-bouté afin de tenir la tête première le plus solidement possible, le riveur vient frapper l’extrémité du rivet permettant ainsi de remplir le trou à l’intérieur de l’assemblage. Le surplus est refoulé dans la bouterolle donnant sa seconde tête arrondie au rivet. En refroidissant, le métal se rétracte assurant le serrage et l’étanchéité de l’assemblage.
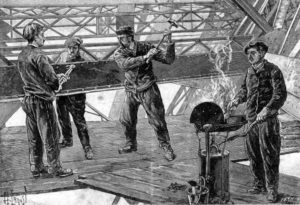
Beaucoup d’infrastructures en Europe et dans le Monde ont été réalisées par la méthode du rivetage à chaud et sont, aujourd’hui encore en service, certaines sont classées monument historique et même au Patrimoine Mondial de l’UNESCO : comme la Tour Eiffel et le Pont Maria Pia (Portugal), toutes les deux réalisées par Eiffel. Ce bel héritage a passé les décennies et est toujours présent aujourd’hui grâce à la solidité de la technique du rivetage.
Quelques entreprises subsistent encore aujourd’hui et entretiennent ce savoir–faire vieux de plus de 150ans. L’apprentissage du métier se fait par compagnonnage et la transmission du savoir des plus anciens aux plus jeunes se fait au fur et à mesure des chantiers, c’est notamment le cas à la SNCF. Il faut savoir que, par exemple, pour savoir faire des rivets selon les règles de l’art, il faut compter entre 2 à 3ans de pratique. 4 équipes de cheminots représentant 30 agents expérimentés aux techniques de réparations des ponts métalliques (R.P.M) notamment de rivetage mais également de vérinage sillonnent la France entière et réalisent près de 50 chantiers par an. Ces agents sont notamment intervenus sur les viaducs de Garabit, Rouzat, Neuvial et bien d’autres ouvrages réalisés par G. Eiffel. Toutes les réparations réalisées respectent les méthodes de construction d’origine.
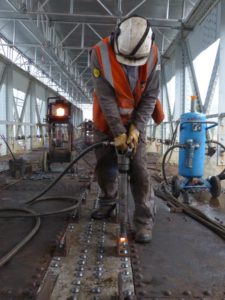
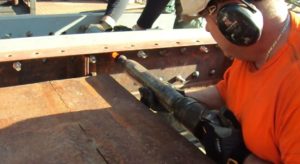
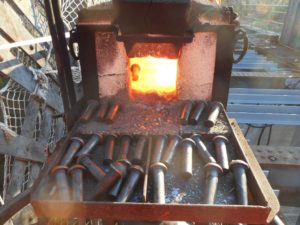
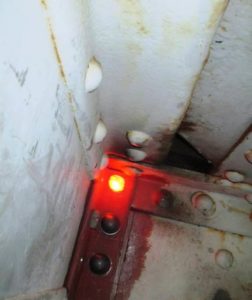
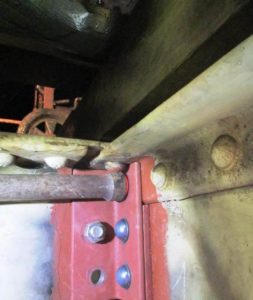
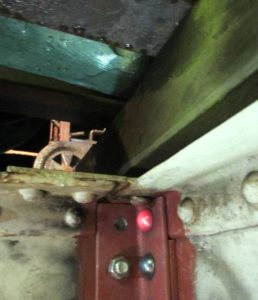
Damien LHÔTE
Maitre d’œuvre des équipes de Réparations des Ponts Métalliques (R.P.M)